Fluidized Bed Powder Coating Technology: A Comprehensive Overview
Fluidized bed powder coating is a versatile and efficient method of applying a protective and decorative layer to a wide range of substrates. This blog post aims to provide a comprehensive overview of fluidized bed powder coating, its historical evolution, underlying principles, applications, recent advancements, and its impact on various industries.
Historical Evolution of Fluidized Bed Powder Coating
Fluidized bed powder coating has its roots in the early 1960s when the first patent for the process was filed. Initially, it was employed primarily in the automotive industry to coat small parts such as valve covers and air cleaner housings. Over the decades, with continuous research and development, the technology has evolved into a sophisticated and widely adopted coating method for various industries.
Underlying Principles of Fluidized Bed Powder Coating
The essence of fluidized bed powder coating lies in the principle of fluidization, which involves suspending fine powder particles in a stream of air. This is achieved by passing a controlled flow of compressed air through a porous plate at the bottom of a coating chamber, creating a fluid-like state where the powder particles behave as if they were a liquid. The substrate to be coated is preheated and dipped into this fluidized powder bed, allowing the particles to adhere uniformly to its surface. Subsequent curing of the coated substrate results in a durable, seamless finish.
Applications of Fluidized Bed Powder Coating
One of the critical strengths of fluidized bed powder coating is its versatility in handling a wide range of substrates. From metal components to plastics, ceramics, and even glass, this method has found applications in various industries. Notable examples include the automotive sector, where it is used for coating suspension components and chassis parts, and the furniture industry, where it provides a durable and aesthetically pleasing finish to metal and wooden surfaces.
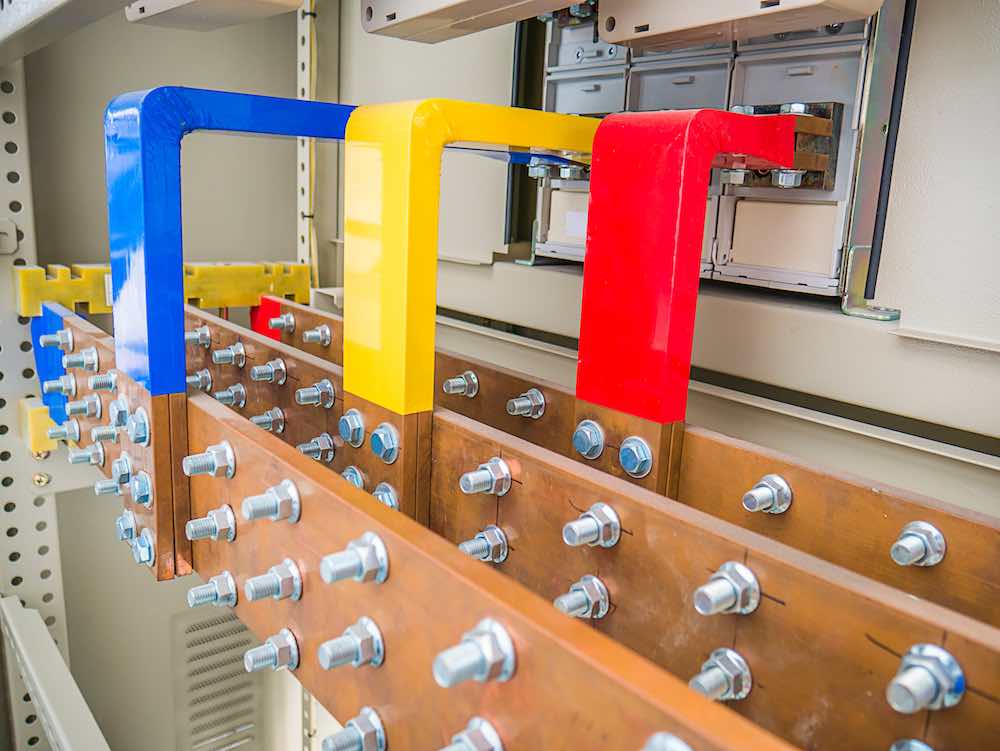
Benefits of fluidized powder coating
Fluidized bed powder coating offers a range of benefits that make it an attractive option for various industries and applications. Here are some of the key advantages of using fluidized bed powder coating:
Uniform Coating Thickness: Fluidized bed powder coating provides an even and consistent coating thickness, ensuring a smooth and flawless finish. This eliminates issues such as sags, drips, and runs commonly associated with liquid coatings.
High Transfer Efficiency: The process boasts high transfer efficiency, meaning a significant portion of the powder is deposited onto the substrate, minimizing waste. This efficiency can result in cost savings due to reduced material usage.
Wide Range of Substrate Compatibility: Fluidized bed powder coating is versatile and can be used on various substrates, including metals, plastics, ceramics, and glass. This versatility makes it applicable across numerous industries.
Excellent Adhesion and Durability: The fluidized bed process ensures excellent powder adhesion to the substrate, resulting in a durable and long-lasting finish. This durability makes it particularly suitable for applications where the coated surface may be exposed to harsh environmental conditions.
Environmentally Friendly: Unlike solvent-based liquid coatings, which release harmful volatile organic compounds (VOCs) into the atmosphere, powder coatings emit negligible levels of VOCs during application. This is a significant environmental benefit, as it contributes to reducing air pollution and promoting a safer working environment.
Continued below …
Do You Need Help With Manufacturing?
Our team of seasoned manufacturing specialists is ready to understand your unique needs and craft a tailor-made plan to optimize your product creation. We offer a comprehensive suite of manufacturing solutions, encompassing both domestic (USA) and international (Mexico) options. Let’s unlock the full potential of your manufacturing process. We’ll guide you every step of the way. Contact us for a complementary consultation.
Reduced Health and Safety Risks: Because it doesn’t involve using solvents, there are fewer health and safety risks associated with fluidized bed powder coating. This creates a safer working environment for operators and reduces the need for specialized ventilation and exhaust systems.
Ease of Automation: Fluidized bed powder coating can be easily integrated into automated production lines, allowing for high-volume, consistent, and efficient coating processes. This makes it a preferred choice for industries with large-scale manufacturing operations.
Versatility in Finish Options: Powder coatings are available in a wide range of colors, textures, and finishes, allowing for customization to meet specific aesthetic requirements. This versatility makes fluidized bed powder coating suitable for functional and decorative applications.
Reduced Maintenance Requirements: Once cured, powder coatings tend to be more resistant to chipping, scratching, and corrosion than traditional liquid coatings. This leads to lower maintenance requirements and longer service life for coated products.
Recyclability and Waste Reduction: Over-sprayed powder from the coating process can be collected and reused, minimizing waste and reducing material costs. Additionally, because powder coatings don’t contain solvents, there is no need for expensive and complex waste disposal systems.
Regulatory Compliance: Powder coatings often meet or exceed environmental regulations and industry standards, making them a compliant choice for manufacturers seeking to adhere to strict environmental guidelines.
Recent Technological Advancements
Recent advancements in fluidized bed powder coating technology have further enhanced its efficiency, flexibility, and performance. One notable development is the introduction of electrostatic fluidized bed systems, where an electrostatic charge is applied to the powder particles, resulting in improved adhesion and reduced overspray. Additionally, advances in powder formulation have led to coatings with enhanced durability, corrosion resistance, and specialized properties such as low-friction and anti-microbial capabilities.
Environmental Considerations and Sustainability
In an era where sustainability is paramount, fluidized bed powder coating stands out as an eco-friendly coating option. Unlike solvent-based liquid coatings, which release harmful volatile organic compounds (VOCs) into the atmosphere, powder coatings emit negligible levels of VOCs during application. This not only safeguards the environment but also ensures a safer working environment for operators. Furthermore, the recyclability of over-sprayed powder contributes to reducing waste and overall environmental footprint.
Fluidized bed powder coating has emerged as a transformative technology in the surface finishing industry, offering a versatile, efficient, and environmentally friendly alternative to traditional coating methods. Its evolution from humble beginnings to a sophisticated process capable of handling diverse substrates is a testament to the continuous innovation and research in this field. With recent advancements further enhancing its capabilities, fluidized bed powder coating is poised to play a pivotal role in shaping the future of surface finishing across many industries.
Additionally, fluidized bed powder coating is a versatile and efficient method for applying protective finishes to various surfaces. This process involves suspending finely ground particles of coating material in air, creating a fluidized bed that behaves like a liquid. When a preheated substrate is immersed into this bed, the particles adhere to its surface, forming a uniform and durable coating. One of its primary advantages is ensuring a uniform coating thickness, even on complex and irregularly shaped objects. This characteristic eliminates issues like sags or drips, guaranteeing a consistently high-quality finish. Additionally, fluidized bed coating is remarkably material-efficient, allowing excess powder to be collected, reclaimed, and reused, thereby minimizing waste and reducing overall coating costs.
Another notable benefit is its adaptability across various substrates, including metals, glass, ceramics, and select plastics. This versatility makes fluidized bed powder coating suitable for multiple industries and applications. Moreover, the resulting coating offers outstanding corrosion protection, making it invaluable in environments where safeguarding against harsh elements is paramount. Its excellent impact resistance further solidifies its utility for surfaces subject to physical stresses. Regarding sustainability, fluidized bed powder coating shines as an environmentally friendly option. It lacks solvents and does not emit harmful Volatile Organic Compounds (VOCs), reducing air pollution and safeguarding worker health.
Furthermore, the process boasts a swift curing time, enabling high production rates and expedited turnaround times. Additionally, it provides flexibility in finish and texture, ranging from smooth and glossy to textured and matte, allowing for a wide array of aesthetic options. Overall, fluidized bed powder coating presents a highly efficient, cost-effective, and environmentally conscious solution for achieving durable and visually appealing surface finishes across a diverse range of substrates and applications.
Prince Manufacturing fluidized bed powder coating services at its US and Mexican facilities. Contact us for details of how we can help you.